Le Lean management est un concept qui consiste à rendre un processus le plus simple possible en ne conservant que les étapes qui représentent de la valeur ajoutée pour le Client du processus. Autrement dit, ce qui contribue à “ce pour quoi le Client est prêt à payer”.
Le processus en question peut être un processus de production, de réalisation d'un service ou encore de traitement d'une information.
Dans cet article, nous définirons cette méthodologie, ses principes, ainsi que son contexte d'utilisation.
Ensuite, je vous donnerai des conseils clés pour réussir son déploiement, étude de cas à l'appui.
Définition du Lean management
Le Lean management est un système d'organisation qui regroupe l'ensemble des principes d'amélioration continue de la performance qui peuvent être applicables dans n'importe quelle organisation.
Cette méthodologie a pour objectif de :
- Améliorer les processus de production dans les industries : Puisqu'elle influence l'ordonnancement et la planification de production en promouvant des méthodes et des principes qui visent à réduire le gaspillage, à maximiser l'efficacité opérationnelle et à s'adapter plus rapidement aux changements de la demande du marché
- Optimiser la réalisation d'un service : Par exemple l'acheminement d'un colis chez un client, ou bien encore le parcours d'un patient réalisant des examens dans un hôpital
- Rendre plus efficace le traitement d'une information : Par exemple l'enregistrement d'une commande client
Plusieurs concepts historiques, mais qui sont spécifiques au domaine de la production, sont regroupés sous le terme de Lean Manufacturing.
Parmi ces concepts, l'un des plus essentiels est le Taux de Rendement Synthétique (TRS).
Avec la diffusion de la méthodologie en question dans l'ensemble des organisations, de nouvelles démarches spécifiques ont également vu le jour, qui sont par exemple connues sous le nom de Lean Office (appliqué aux tâches administratives), ou Lean Engineering (appliqué à la conception).
Quels sont les principes du Lean management ?
Il existe 11 principes du Lean, à savoir :
- La qualité, coûts et délais
- Le Juste-à-temps
- Le temps de Takt
- Les flux tirés
- L'autonomation
- L'andon
- La séparation du travail des hommes et des machines
- Le nivellement
- Kaizen
- Le travail Standard
- Et la stabilité
Pour mieux comprendre ces principes, je vous propose d'analyser la représentation qui en est faite par Toyota, l’un des pionniers et leaders dans le déploiement de cette démarche.
Toyota représente ce concept sous forme de “maison du Lean” ou de “temple” :
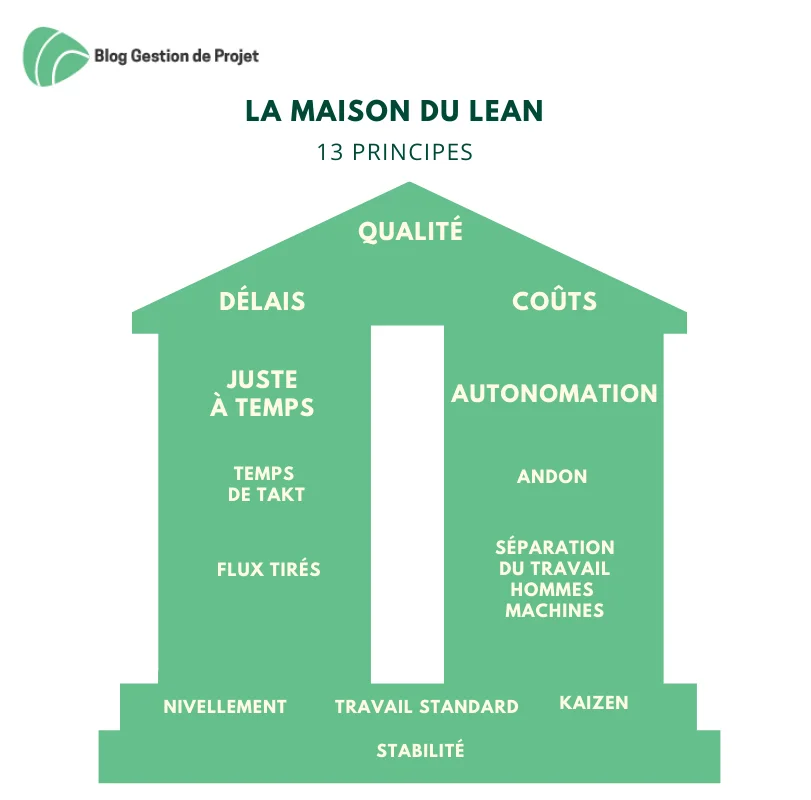
Décrivons cette maison en partant du toit, c'est-à-dire de la finalité, pour découvrir ensuite ses concepts clés et principes.
Il s’agit donc de supprimer un maximum d'étapes de processus qui ne contribuent pas à la valeur ajoutée du produit ou du service pour laquelle le Client est prêt à payer.
1) Triangle « Qualité, Coûts, Délais »
Le Lean Management aura donc pour vocation d'entraîner une diminution des défauts et rebuts qui ne peuvent être vendus aux Clients, avec pour conséquence une amélioration de la QUALITÉ.
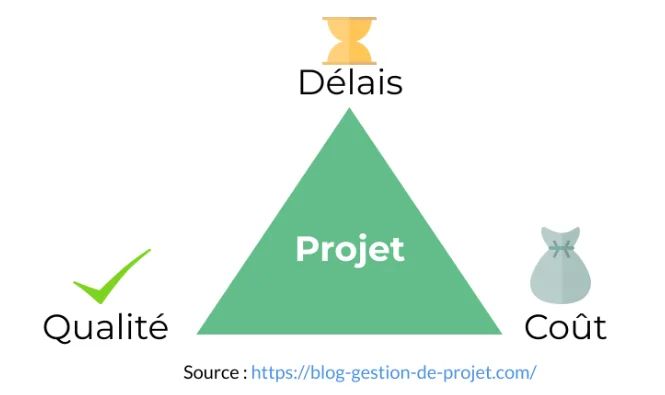
Et par ailleurs, par la suppression d'étapes inutiles, nous allons provoquer à la fois une diminution des DÉLAIS de livraison au Client, ainsi qu'une diminution des COUTS.
Maîtrisez la triple contrainte avec ce kit de gestion de projet :
Nous voyons ensuite sur cette maison que ce toit est soutenu par deux piliers : le JUSTE-A-TEMPS et l'AUTONOMATION.
2) Juste-à-temps, Temps de Takt, et Flux tirés
Le JUSTE-A-TEMPS consiste à ne réaliser une étape d'un processus qu’au moment où son résultat est requis par l'étape suivante. Par exemple : achever la finition d'un siège de voiture juste avant son montage sur la voiture.
Autrement dit, il s’agit de supprimer ou de limiter tous les stocks intermédiaires.
En pratique, on conserve souvent un stock intermédiaire minimal dont la taille est calculée en fonction du niveau de variabilité que l'on n'arrive pas encore à maîtriser.
Le JUSTE-A-TEMPS fait appel aux principes du Temps de Takt qui représente le rythme lissé de la demande du Client, et du Flux Tirés qui organisent le déclenchement d'une étape du processus par la commande du Client.
3) Autonomation, Andon, et séparation du travail des hommes et des machines
Le second pilier, l'AUTONOMATION, aussi appelée Jidoka, peut être considéré comme la composante « Qualité » de la maison.
L'AUTONOMATION vise à rendre immédiats la détection des défauts et l'arrêt de la production si un défaut survient, voire à rendre impossible l'occurrence d'un défaut.
Ce principe s'appuie :
- Sur l'Andon, qui est le principe d'alerte sur défaut
- Et sur la séparation du travail des hommes et des machines : les méthodes utilisées pour identifier et résoudre les problèmes étant distinctes selon qu'il s'agisse de travail humain ou d'opérations réalisées par une machine ; il serait très complexe de chercher à optimiser une opération où se mélangent à la fois la machine et l'intervention humaine. Pour les machines, c'est principalement la démarche TPM, ou Total Productive Maintenance, qui est appliquée.
4) Nivellement, Kaizen, et Travail Standard
Les deux piliers précédents ne peuvent être bâtis que sur une base solide. Cette base consiste en trois principes :
- Le NIVELLEMENT de la production, que l'on pourrait traduire de manière un peu simpliste par « produire un peu de tout, tout le temps » (notion de mix produits)
- Le KAIZEN, un terme japonais qui signifie littéralement « Amélioration Continue », c'est-à-dire la recherche du progrès permanent
- Et le TRAVAIL STANDARD qui constitue la base du progrès, en ce sens qu'il représente le référentiel de base pour le travail manuel effectué sur le processus, et qu'il sera amené à évoluer au rythme du Kaizen
5) Stabilité
Enfin, comme cette discipline nécessite une adaptation très fine à l'environnement de l'entreprise, un maximum de STABILITÉ est nécessaire parmi les matières premières entrantes, la main d’œuvre, les moyens utilisés, les méthodes et le milieu (l’œil affûté aura reconnu ici les 5M).
Avantages et limites
Parmi les avantages de l'approche, on trouve les gains en argent et en temps, la stabilisation de la charge de travail, et l'appropriation des méthodes par les salariés.
De l'autre côté, nous pouvons considérer comme limites, ou plutôt mauvais usages : le fait de considérer qu'il s'agit d'outils utilisés séparément et non de concepts, ou encore le fait de ne pas prendre en compte la santé des travailleurs.
Voyons ces éléments un par un :
1) Les avantages
Cette méthodologie menée correctement aura un impact significatif sur différents aspects de l'organisation :
- Gains économiques : en supprimant tout ce qui est « gaspillage », tout ce qui ne représente pas de Valeur Ajoutée pour le Client, les coûts liés à ces gaspillages vont disparaître et entraîner une amélioration des résultats financiers de l'organisation
- Gains en temps d'écoulement du processus : de la même façon, la suppression des gaspillages va accélérer le flux du processus et va permettre de délivrer le produit ou le service au Client plus rapidement
- Stabilisation de la charge de travail : paradoxalement, cette accélération du flux ne va pas se traduire par une cadence de travail plus importante pour les salariés, mais au contraire par une stabilisation et un lissage de la cadence, conséquence de la suppression des à-coups
- Meilleure appropriation des méthodes de travail par les salariés : en impliquant les équipes du terrain dans les chantiers d'amélioration et en communiquant suffisamment, nous allons donner du sens et provoquer une meilleure appropriation des nouvelles méthodes de travail.
2) Les mauvais usages
Il n'y a pas à proprement parler de limites ou d'inconvénients.
Par contre, il y a de mauvaises façons de déployer le Lean Management qui peuvent provoquer plus de dégâts que de gains.
2.1) Considérer qu'il s'agit d'un ensemble d'outils et non de concepts
Il ne s'agit pas d'un ensemble d'outils, mais d'un ensemble de concepts.
Je vous explique pourquoi dans l'étude de cas plus bas.
2.2) Ne pas prendre en compte la santé des travailleurs
Si l'on ne prend pas certaines précautions, le Lean management peut entraîner une dégradation des conditions de travail.
Comme nous l'avons vu plus haut, il n'y a pas une façon unique de déployer cette démarche sur un périmètre.
L'important est d'appliquer les concepts de la manière la mieux adaptée à l'environnement de travail à un moment donné.
Il n'y aurait aucun sens à déployer une telle démarche sans prendre en compte la santé des travailleurs.
Cette recherche de la “manière la mieux adaptée” doit donc prendre en compte la santé physique (ergonomie, ergomotricité) et mentale (charge mentale, isolement à éviter) des collaborateurs.
Des experts existent dans ces domaines et ils peuvent être sollicités durant les projets d'amélioration.
Par ailleurs, de plus en plus de formations sur le sujet traitent à la fois de l'aspect « performance » et de l'aspect « santé au travail », ce qui permet aux coordinateurs dans les entreprises d'être relativement autonomes dans ce domaine.
Voici le résumé des bénéfices et limites de l'approche :
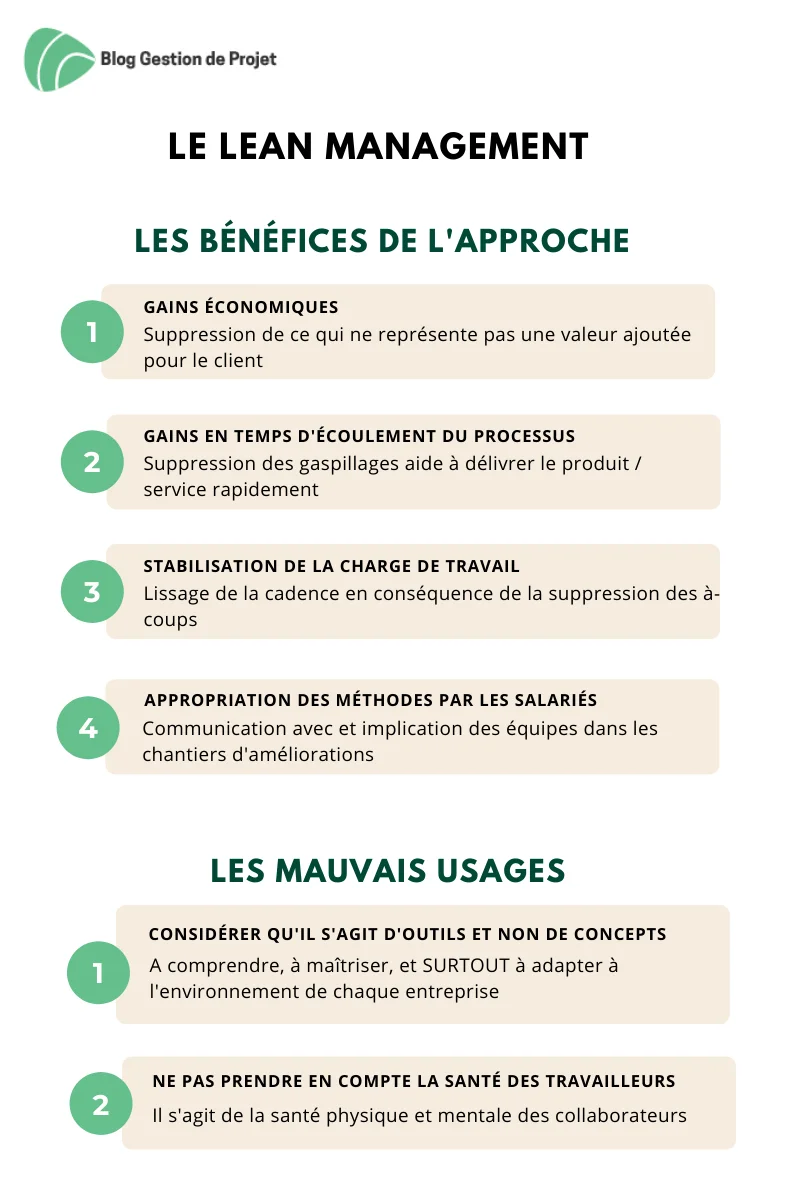
Cas pratique du lean management
Voyons ci-après un exemple réel pour bien assimiler l'importance du concept.
Voici une explication par l'histoire (presque) vraie de l'entreprise Demain-jexcelle qui fabrique des yaourts et qui rencontre des problèmes de production.
Les clients de cette entreprise sont de moins en moins souvent livrés dans les délais, et sont victimes de ruptures de stocks.
Jean, le Directeur Général de Demain-jexcelle, vient de lire un article au sujet de la méthodologie en question et de ce qu'il a apporté dans les industries qui l'ont mis en place.
Il lit aussi que Toyota fait figure d'exemple dans ce domaine.
Visite d'observation dans l'usine
Comme Jean veut obtenir des résultats rapides, il décide d'organiser une visite dans l'usine Toyota toute proche, accompagné par son Responsable Production et son Responsable Logistique, afin de s'inspirer de ce qui a été mis en place.
La visite dure quelques heures. Toyota présente une de ses lignes de production avec un certain nombre d'outils du domaine qui ont été mis en place.
Inspiration de l'utilisation de la méthode KANBAN
Les résultats de production sur cette ligne sont excellents. Ce qui impressionne le plus Jean et ses collaborateurs, c'est l'utilisation de cartes Kanban qui permet une gestion des flux optimisée sur la ligne.
Jean et son équipe prennent énormément de photos des tableaux où sont regroupées ces cartes, et Toyota les autorise même à emmener quelques exemples de cartes.
Application du procédé observé
De retour à l'usine de yaourts, Jean donne comme objectif à ses équipes de mettre en place le même système Kanban que Toyota sur l'ensemble de leurs lignes d'ici à une semaine.
Tout le monde s'y emploie avec énergie et, au prix de quelques heures supplémentaires effectuées, un système strictement identique à ce qui a été vu chez Toyota est opérationnel dans les délais demandés par Jean.
Constatation de résultats insatisfaisants
Dans les jours qui suivent, Jean et son comité de direction suivent avec une certaine excitation leurs indicateurs de performance dans l'attente d'une nette amélioration, afin de pouvoir rassurer leurs clients.
Mais un mois plus tard, malgré une semaine de démarrage qui avait pourtant été prometteuse, les résultats ne sont nullement meilleurs qu'avant la mise en place du système Kanban.
Revisite d'exploration à l'usine
Convaincus qu'ils ont dû passer à côté d'un élément important de l'utilisation du tableau Kanban, Jean demande à Toyota s’ils peuvent revenir visiter leur usine.
C'est chose possible la semaine suivante et, de retour sur la même ligne de production de Toyota, Jean et son équipe sont extrêmement surpris de ne plus y voir le tableau Kanban.
Compréhension du fait qu'il n'y a pas une solution pour tout
Toyota utilise à présent un autre système. “Ce n'est pas ce que nous avions vu la dernière fois”, signale Jean au superviseur Toyota qui les accompagne. “Ce que vous nous aviez montré n'était donc pas la bonne solution pour gérer les flux de cette ligne”.
La réponse du superviseur : “Si. Ce que vous aviez vu la dernière fois était la solution qui nous convenait le mieux à ce moment-là.
Aujourd'hui, suite à nos démarches d'amélioration continue en place dans l'entreprise, nous avons adapté nos outils à nos besoins actuels. Et dans quelques mois, nos outils auront encore évolué”
Moralité de l’histoire
Les entreprises les plus performantes et celles qui ont réussi l'implémentation d'une telle démarche sont généralement connues.
Beaucoup viennent les visiter pour “prendre exemple” sur ces leaders en espérant obtenir les mêmes résultats... qui la plupart du temps ne sont pas au rendez-vous.
La raison vient d'une incompréhension courante de cette méthodologie.
Il ne s'agit pas d'outils tout faits qu'il suffit de reproduire.
C'est un ensemble de concepts qui doivent être compris, maîtrisés, puis mis en œuvre et adaptés à l'environnement spécifique de chaque entreprise.
Les pionniers dans ce domaine considèrent que son déploiement nécessite une très bonne compréhension des détails des processus de l'entreprise, afin de mettre en place les solutions les plus adaptées possibles.
Peut-on espérer des gains financiers directs ?
La réponse est non !
S'il ne fait aucun doute qu'une démarche Lean apportera des gains à l'organisation qui la met en place, il ne faut pas tomber dans le piège de vouloir la piloter exclusivement à partir d'indicateurs de gains financiers directs.
Le choix des chantiers à mener est davantage une affaire de compréhension du contexte de l'entreprise et de conviction, qu'un calcul financier basé sur l'économie qui sera générée.
En effet, de nombreuses améliorations ont un impact qui n'est pas mesurable de manière directe financièrement.
Voici quelques exemples qui prouvent que l'on ne peut pas mesurer l'impact financier direct d'une telle démarche :
1) Gain lié au déploiement de la TPM
Vous mettez en place une politique de maintenance préventive des équipements critiques qui était jusque-là inexistante.
Cela va amener des coûts supplémentaires, mais vous ne pouvez pas calculer le gain lié aux pannes qui ne se produiront pas. Pourtant, le préventif est nécessaire.
2) Gain lié à l'optimisation des flux de production
Vous faites un gros travail d'optimisation de vos flux qui vous permet de faire baisser le temps d'écoulement entre la commande du client et la livraison du produit de 30 jours à 10 jours.
Comment mesurez-vous l'impact financier des commandes supplémentaires que vous recevrez de la part de Clients qui vous ont choisi pour cette performance par rapport à un autre concurrent ?
3) Gain lié à l'amélioration d'un poste de travail
Vous aménagez un poste de travail, ce qui a pour conséquence de faciliter le travail d'un opérateur qui peut désormais être plus vigilant sur son activité de contrôle qualité, évitant ainsi certaines non-conformités, certains blocages de produits et certaines réclamations Clients.
Comment estimez-vous le gain financier de cette amélioration ?
Si votre Directeur vous donne comme objectif de mettre en place un plan d'actions chiffré visant à diminuer les coûts de votre organisation de 1%, malheureusement, vous risquez de ne jamais lancer les trois exemples d'améliorations ci-dessus, car vous n'arriverez pas à les « vendre ».
6 bonnes pratiques
Une organisation qui souhaite passer au Lean, se doit d'appliquer les principes de l'amélioration continue.
Voici les 6 bonnes pratiques essentielles pour mettre en place le lean management :
1) L'Engagement de la Direction
Inutile de lancer une démarche dès la fin de la lecture de cet article si vous n'avez pas le soutien de votre Direction.
Sa mise en place nécessite souvent un changement radical de culture dans l'entreprise et le département en charge de son déploiement, surtout s'il est nouvellement créé, n'a pas naturellement la légitimité nécessaire pour intervenir auprès des différents services de l'entreprise et transformer les processus existants.
Un « mandat » donné à l'équipe par la Direction est indispensable.
Un certain nombre d'organisations se sont habituées à fonctionner en silos et, pour décloisonner les choses, seul le dirigeant à la main sur l'intégralité du périmètre.
2) L'implication du Personnel
Pour autant, « engagement de la Direction » ne signifie pas que les transformations doivent être décrétées par les dirigeants de l'entreprise et appliquées de manière directive.
L'implication du personnel est nécessaire au moins deux titres :
2.1) Il est derrière la création de la valeur ajoutée
Nous avons vu que le Lean est axé autour de la Valeur Ajoutée apportée au Client.
Or, dans l'entreprise, les personnes qui « manipulent » le produit ou le service délivré au Client, ceux qui le transforment et apportent la Valeur Ajoutée, ce sont les personnes du terrain.
Ce sont eux qui connaissent les vrais problèmes et qui souvent ont déjà les solutions.
2.2) Il met en œuvre les chantiers d'améliorations
La mise en œuvre des améliorations, notamment l'application des standards de travail, passe, elle aussi, par les opérateurs, par ceux qui réalisent le travail.
Leur fierté et leur persévérance à les appliquer seront d'autant plus fortes qu'ils en auront été à l'initiative ou qu'ils y auront contribué.
3) Gemba
Afin de mener à bien les démarches d'amélioration, les groupes de travail seront composés à la fois des équipes du terrain - qui amènent leurs expériences et leurs expertises - et des équipes de services Lean ou Amélioration Continue qui vont apporter la méthodologie. Les deux profils étant complémentaires.
Pour jouer pleinement leur rôle, ces équipes ainsi que le Management doivent être présent la majorité de leur temps sur le terrain, le « Gemba ».
Ce terme japonais peut être traduit littéralement par « là où se passe l'action ».
Il est couramment utilisé dans ce domaine, car il exprime le rôle primordial de l'observation des processus dans les démarches d'amélioration.
C'est notamment par la longue observation, patiente et répétée que les personnes formées dans ce domaine vont pouvoir identifier les « Mudas », autre terme japonais que l'on peut traduire par « gaspillage » et qui évoque les non-valeurs-ajoutées que l'on souhaite retirer de nos processus.
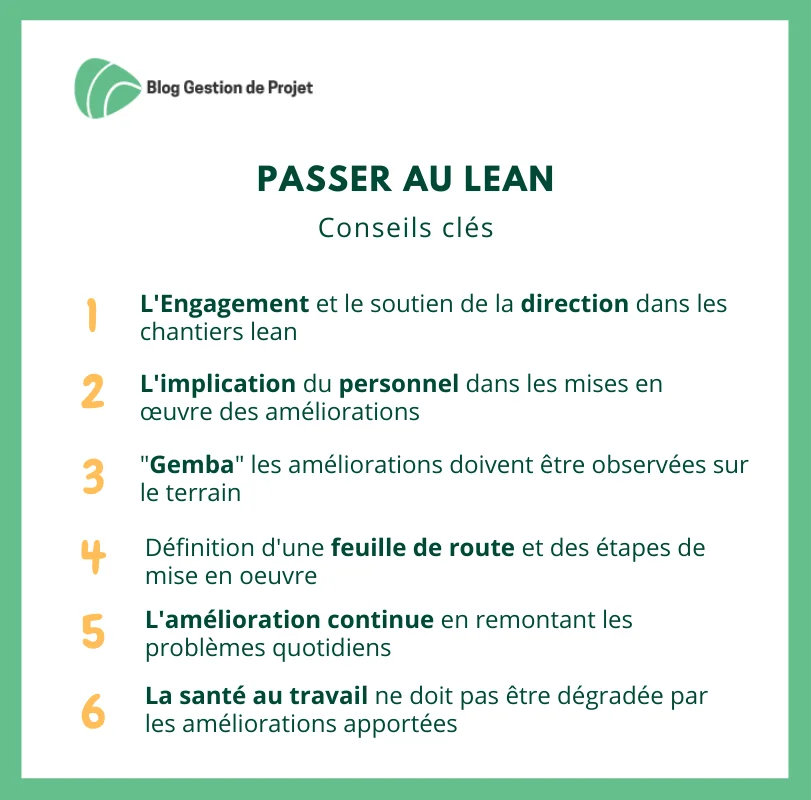
4) Définition d'une feuille de route
Les chantiers à mener ne doivent pas être décidés au moyen d'un brainstorming, ou suite à une visite dans une autre entreprise qui a mis en place un outil qui nous paraît intéressant.
Il s'agit d'abord de faire un diagnostic de l'état actuel de l'entreprise, au moyen d'outils tels que le Value Stream Mapping (VSM, ou analyse de la chaîne de valeur).
Puis vient la définition de « où l'on veut amener l'entreprise dans les prochaines années ».
Et à partir de là seront définies les étapes et les chantiers d'amélioration nécessaires.
5) L'amélioration continue
Il est important de concevoir qu'une organisation Lean n'est pas un état binaire, et que ce concept ne se résume pas à une démarche ou à un résultat.
Ce concept, et en particulier celui du Kaizen, est le principe de l'amélioration permanente.
Par conséquent, parmi les rituels incontournables d'une entreprise qui s'est lancée dans ce domaine, nous allons retrouver des points quotidiens de résolution de problèmes animés par des équipes pluridisciplinaires.
Ces équipes vont analyser chaque jour le ou les problèmes principaux de la veille et, en proposant les solutions pérennes adéquates, vont contribuer au progrès permanent de l'organisation.
6) La santé au travail
"Le travail, c'est la santé" (Henri Salvador, 1965).
Nous l'avons évoqué dans un paragraphe précédent : il peut arriver que des modifications apportées à un poste de travail dans le cadre d'un chantier aient un impact négatif sur la santé des travailleurs.
C'est un aspect qu'il ne faut absolument pas négliger.
En fait, non seulement il faut s'assurer que les améliorations apportées aux postes de travail ne dégradent pas l'ergonomie du poste, mais la santé au travail peut même être la motivation première pour le lancement d'un chantier d'amélioration.
Même les « petites gênes » dont on pourrait penser qu'elles ne portent pas à conséquence sur la santé vont forcément au moins avoir un impact sur la concentration de la personne sur ses tâches, et il y a tout à gagner à chercher à les éliminer.
Conclusion
Le Lean Management et ses déclinaisons (Manufacturing, Office ou Engineering) sont devenus incontournables dans les organisations d'aujourd'hui, et pas uniquement dans les industries.
Comme toute démarche en mesure d'améliorer significativement la performance d'une entreprise, il ne s'agit pas d'une panoplie d'outils simplistes qui peuvent être mis en œuvre du jour au lendemain.
Il s'agit de concepts de Management et d'Organisation dont le déploiement nécessite l'engagement de la Direction et une bonne expertise de la part des équipes chargées de la mise en œuvre.
Nous aurons l'occasion dans de prochains articles d'aller plus en avant dans cette aventure en explorant plus en détails certains de ses concepts-clés.
Très bon article!
Merci pour ce retour 🙂