Un Standard de Travail définit la meilleure façon, connue à ce jour et partagée par tous pour effectuer une tâche. Dans une démarche Lean, c’est l’un des concepts de base. Il s'agit de la façon dont les tâches doivent être réalisées, et contribue au résultat final en termes de Qualité, Délais et Coûts. On retrouve bien d'ailleurs ce concept dans le socle de la "Maison du Lean" de Toyota.
Dans cet article, nous allons expliquer ce que sont les Standards de travail et leur importance. Nous verrons comment ces standards permettent d'optimiser la performance opérationnelle, d'éliminer les gaspillages et d'améliorer la qualité des produits ou des services.
Pourquoi est-il nécessaire dans une démarche Lean ?
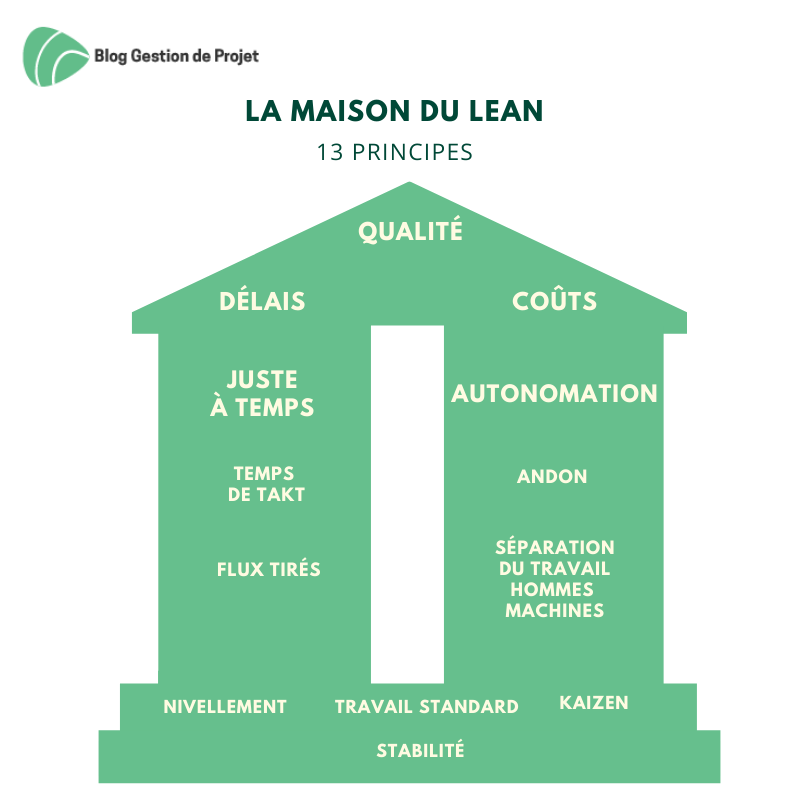
L'un des axes de travail dans une démarche Lean est de s'attaquer à la réduction de la variabilité dans les processus.
La variabilité, c'est le fait que, par la réalisation d'une même tâche composée d'activités a priori semblables et répétitives, le résultat obtenu va varier, jusqu'à parfois générer des défauts ou des écarts impactants.
Le standard de travail va permettre de réduire les variations dans la réalisation des activités, avec pour conséquence de stabiliser le résultat. Cette stabilité facilitera la distinction entre le normal et l'anormal.
Il va donc contribuer à assurer le niveau de performance en Sécurité, Qualité, Délais et Coûts, à réduire la variabilité, à assurer la reproductibilité des opérations, et donc à garantir la qualité du résultat.
Cette reproductibilité va également rendre évidents les liens de cause à effet : si l'on décide de jouer sur un paramètre, tout le reste demeurant constant, les conséquences constatées seront donc forcément liées au paramètre modifié.
Enfin, les Standards permettront la formation des nouveaux opérateurs et la réalisation d'audits, points que nous aborderons plus loin dans cet article.
Qu'est-ce que le Travail Standard plus concrètement ?
La standardisation fait partie des étapes d'accompagnement à la transformation Lean au sein d'une organisation.
Si on revient sur la définition donnée en introduction :
"Les standards de travail sont des normes de travail qui définissent la meilleure façon, connue à ce jour et partagée par tous pour effectuer une tâche".
Tous les mots sont importants dans cette définition :
- "la meilleure façon" :
Il doit correspondre à une manière efficace de réaliser une tâche, que ce soit au niveau de la sécurité des opérateurs, de la qualité du résultat, du coût (main d'oeuvre, énergie, ...) et du délai de réalisation de la tâche.
- "connue à ce jour" :
On retrouve ici l'idée d'amélioration continue.
S'il doit être scrupuleusement respecté, il ne doit pas être pour autant figé ad vitam aeternam.
Chacun doit être en mesure de proposer des améliorations qui, si elles sont validées, conduiront à une mise à jour du Standard.
Nous reviendrons plus loin dans cet article sur cette dualité entre respect et amélioration du Standard.
- "partagée par tous" :
Il y a deux idées derrière cette notion de "partagée par tous".
Tout d'abord, pour maîtriser la variabilité d'un processus, il est important que chaque opérateur applique le même Standard.
C'est le rôle du Management de veiller à cela.
Et pour que cela soit le cas, il est nécessaire que chaque intervenant soit formé et capable de réaliser les opérations demandées.
Peut-être que pour certaines tâches, un opérateur possédant une technique ou une dextérité particulière sera en mesure de réaliser la tâche plus rapidement ou plus efficacement que ses collègues.
Mais s'il est le seul à pouvoir maîtriser cette technique, alors cela ne peut pas être le Standard et même lui devra s'astreindre à respecter le standard commun "partagé par tous".
Exemples de standards
Des processus peuvent être mis en place pour différents types d'activités.
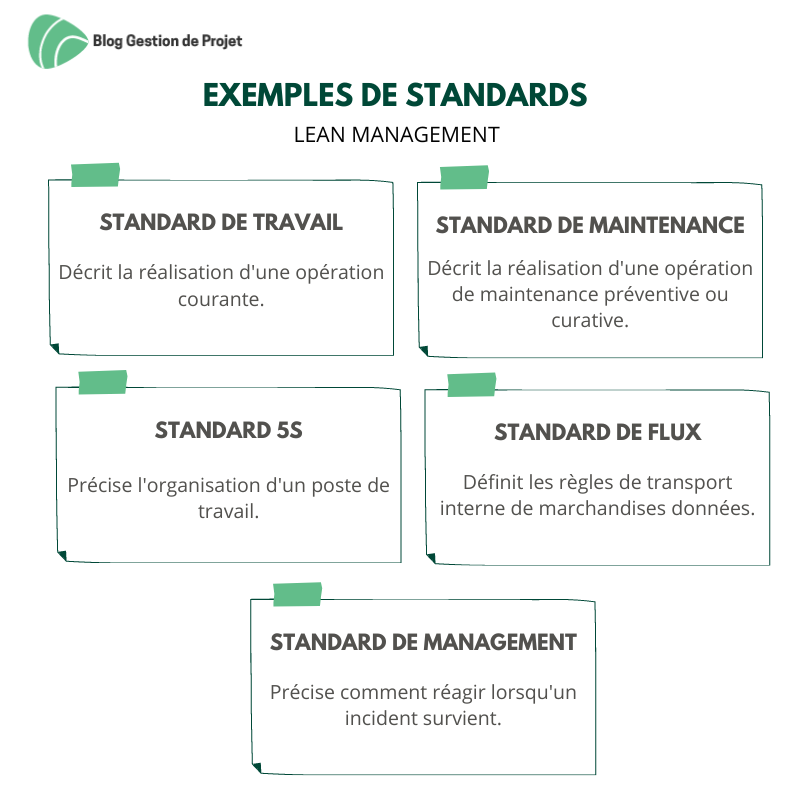
On peut citer par exemple le Standard :
- de travail, qui décrit la réalisation d'une opération courante, par exemple les activités d'un opérateur de production pour la fabrication d'un article donné dans une configuration donnée
- de maintenance, qui décrit la réalisation d'une opération de maintenance préventive ou curative
- 5S, qui précise l'organisation d'un poste de travail
- de flux, qui définit les règles de transport interne de marchandises données
- de management, qui précise comment réagir lorsqu'un incident survient.
Bonnes pratiques pour le définir
1) Clarté et simplicité
Pour qu'il puisse être appliqué efficacement, un Standard de Travail doit être simple, clair et évident.
Il doit coller à la réalité du terrain et du métier.
Pour cela, il est nécessaire qu'il soit construit par/ou avec les personnes qui réalisent les opérations concernées, puis enrichi régulièrement avec leurs expériences vécues sur le terrain.
Comme il servira de base pour la formation, il est aussi utile qu'il puisse permettre de "donner du sens" aux différentes activités qu'il décrit.
Par exemple, si la réalisation d'une opération nécessite une manipulation qui peut sembler contraignante à l'opérateur, il est important de prévoir une courte explication pour faire savoir que cette manipulation a pour but d'éviter un risque de blessure ou encore d'éviter un risque de défaut qualité.
Sinon, l'opérateur à qui la manipulation semblerait arbitraire sera tenté de prendre des "raccourcis" et de ne pas la réaliser.
2) Formation et pratique
Une fois qu'un Standard de travail a été établi, avec la participation des personnes du terrain, le travail n'est pas encore terminé.
En effet, il ne s'agit pas qu'il reste dans un tiroir et ne soit pas appliqué, voire parfois même pas connu par les intervenants concernés.
Cette phase est souvent plus complexe que la création du Standard elle-même.
En premier lieu, il s'agit de former l'ensemble des équipes concernées, sans oublier les intervenants occasionnels (remplaçants, opérateurs polyvalents, managers, ...).
La formation idéale cherchera à donner du sens au contenu (pourquoi on fait cela, pourquoi chaque activité décrite est importante, etc.) et inclut une phase pratique, une évaluation et une traçabilité (émargement des personnes formées).
Ensuite, selon la complexité du Standard, son application en conditions réelles sur le terrain pourra être supervisée par un manager ou un tuteur qui maîtrise parfaitement les opérations concernées, afin d'accompagner la montée en compétences du collaborateur.
Dans les organisations les plus matures dans leur conception du Lean Management, un temps important est dédié à l'observation des opérateurs dans leur application du Standard.
Il ne s'agit pas d'évaluer constamment l'opérateur, mais avant tout de s'assurer qu'il est et reste bien adapté aux personnes et au contexte du poste de travail.
De ces observations peuvent naître des propositions d'amélioration.
L'observation peut être menée par des superviseurs, avec le support de spécialistes en ergonomie et conditions de travail.
3) Audit de standard
Comme l'ensemble des composantes d'une démarche Lean, le Travail Standardisé ne peut être initié que par la Direction qui communiquera sur la démarche et montrera l'importance qu'elle y accorde.
Pour le faire réellement fonctionner, une fois l'élaboration de Standards réalisée et le personnel formé, il reste encore à assurer la bonne application, la continuité et l'amélioration continue de la démarche.
Cela passe par la réalisation régulière d'audits de Standards.
Là aussi, l'ensemble de la ligne hiérarchique doit être impliquée : les chefs de services réaliseront les premiers audits, puis la démarche sera ritualisée en impliquant les managers de proximité qui réaliseront eux des audits quotidiens.
Attention : "audits quotidiens" ne veut pas dire auditer 100% des Standards chaque jour.
La fréquence d'audit de chaque Standard sera à définir en fonction de l'évaluation des risques.
Mais en quoi consiste ce processus d’audit ?
Ici aussi, tout comme les observations évoquées précédemment, il ne s'agit pas d'une évaluation de l'opérateur. Il s'agit d'auditer le Standard.
L'objectif de l'audit et de voir s’il est :
- connu
- compris
- appliqué
- et adapté
Si ces quatre points ne sont pas validés, des actions correctives seront à mettre en place.
Cet audit passe par une phase d'observation des activités réalisées par l'opérateur, puis par un échange avec lui sur ce qui a été observé et son ressenti.
À noter que l'on retrouve ce principe de Standardisation et d'audits dans la démarche 5S.
Le 5S est une méthode en 5 étapes (en japonais, le nom de chacune des étapes commence par un "S", d'où le terme "5S").
Les 3 premières étapes consistent à mettre en œuvre les actions d'aménagement du poste de travail:
- Oter l'inutile
- Ranger
- Nettoyer
La 4ᵉ étape consiste à "standardiser" afin que chaque intervenant sur un périmètre donné ait connaissance de ce qui est attendu.
Une manière simple de standardiser le 5S peut être d'afficher une photo qui représente la zone dans l'état standard.
Enfin, la 5ᵉ étape consiste à "auditer", afin de s'assurer que le Standard 5S est adapté, connu, compris et appliqué.
Progresser grâce au Travail Standard
1) Le standard, base de l'amélioration
Nous l'avons vu plus haut : c’est l’un des concepts de base du Lean Management (cf. la Maison du Lean) et il permet de maîtriser la variabilité des processus.
Lorsque l'on présente ce concept à une population, en particulier dans la culture occidentale, un des inconvénients qui est spontanément cité est que faire appliquer le même Standard à tout le monde nuit à la créativité. C'est faux !
Tout d'abord, il est nécessaire de savoir sur quelles activités la créativité est réellement utile.
Certains dirigeants d'entreprise ou leaders politiques sont connus pour adopter chaque jour la même tenue vestimentaire.
Pourquoi ? Pour ne pas perdre de précieuses minutes chaque jour à se demander si le t-shirt rouge est plus adapté que le t-shirt vert et s'il se marie bien avec le pantalon beige.
Dans leur contexte, ce sujet n'est pas prioritaire, ils le gèrent de façon "standard" et préfèrent focaliser leur réflexion sur les nombreux sujets plus impactants dont ils ont la charge.
Ensuite, le standard n'est pas figé.
L'esprit Lean dans une organisation invite au contraire chaque intervenant à émettre des propositions d'amélioration quant à la réalisation des opérations dont ils ont la charge.
Mais cela ne se fait pas de manière anarchique ou désordonnée.
Généralement, une amélioration sera mise en œuvre via les étapes suivantes :
- un intervenant émet une proposition d'amélioration
- elle est partagée avec l'équipe et validée par le superviseur
- un essai peut être réalisé : il peut s'agir d'un essai limité dans le temps, ou, si le même processus est appliqué par différentes équipes (par exemple, sur différentes lignes de production similaires dans une industrie), il est possible de lancer l'essaie sur un périmètre limité
- si l'essai est concluant, alors le Standard de travail est mis à jour et les équipes sont formées à ce dernier, qui entre ensuite en application.
Il est alors possible de mesurer le gain (en temps, en qualité, en efficacité, ...) entre l'ancien et le nouveau Standard.
Si ce gain peut être mesuré, c'est bien parce que l'on est passé d'une situation dans laquelle un Standard initial était appliqué uniformément à une nouvelle situation où le standard mis à jour est à présent appliqué, lui aussi, uniformément.
Si chacun travaille à sa façon, la forte variabilité qui en découle empêche de mesurer les progrès et donc de savoir vers quelle direction aller pour améliorer les processus.
2) Le "filtre du Standard" dans la résolution de problèmes
Face à un problème, à une non-conformité, à un écart, beaucoup d'organisations appliquent des méthodes de résolution de problèmes telles que les "5 Pourquoi" ou le "DMAIC".
Mais, selon les entreprises, dans parfois plus de la moitié des cas, les écarts sont dus au fait qu'un Standard n'a pas été appliqué.
C'est la raison pour laquelle il est utile, en préalable à toute analyse de problème, d'appliquer ce "filtre".
Modèle du diagramme Ishikawa
Analyse et résolution des problèmes avec la méthode Ishikawa avec des études de cas
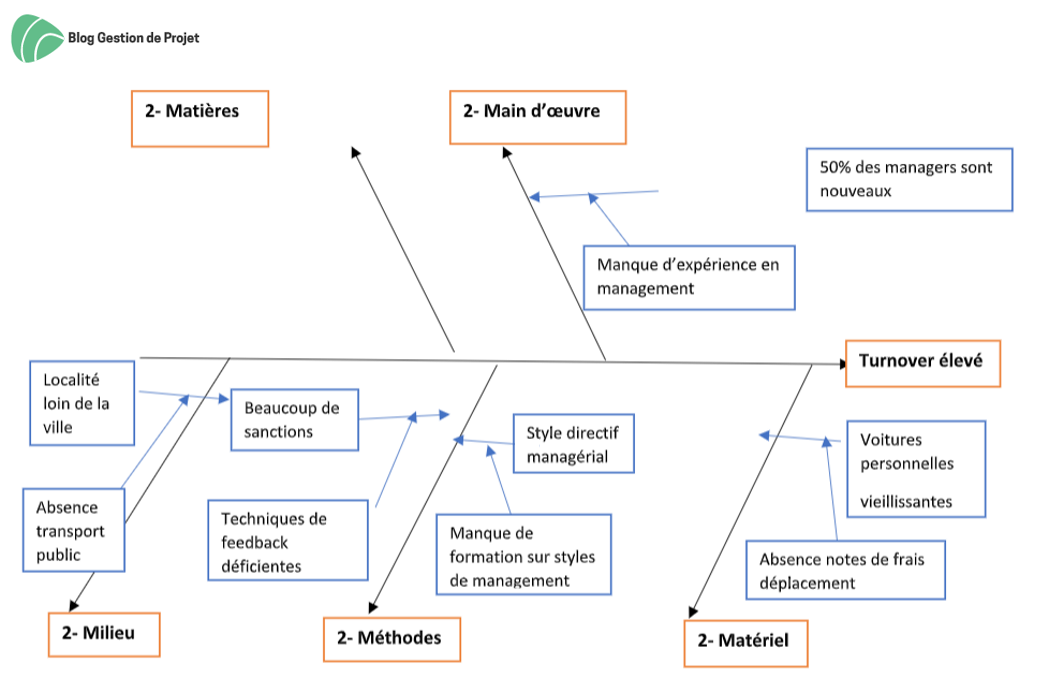
Ce "filtre" consiste à vérifier si la non-application du Standard est la cause du problème ou pas. Il s'agit de poser successivement les questions suivantes :
Le Standard de travail :
- Existe-t-il ?
- Si non, il faut le créer
- Si oui, on passe à la question suivante
- Est-il connu ? (l'opérateur concerné dit-il en avoir connaissance ?)
- Si non, il faut informer/former les équipes à ce principe
- Si oui, on passe à la question suivante
- Est-il compris ? (l'opérateur, lorsqu'il est observé et lorsqu'on lui demande de l'appliquer, le suit-il correctement ?)
- Si non, il faut former l'opérateur, voire le reste de l'équipe
- Si oui, on passe à la question suivante
- Est-il appliqué ? (au moment où le problème est survenu, l'opérateur l’a-t-il appliqué ?)
- Si non, il faut (re)sensibiliser l'opérateur – voire le reste de l'équipe – à son application
- Si oui, on passe à la question suivante
- Est-il adapté au problème rencontré ? (couvre-t-il correctement les opérations qui sont à l'origine du problème ?)
- Si non, il faut former l'opérateur, voire le reste de l'équipe
- Si oui, on passe à la question suivante
Prendre quelques minutes pour répondre à cette suite de questions permet d'identifier si le problème peut être évité simplement en utilisant ce principe.
Une équipe de résolution des problèmes s'avère utile pour gérer efficacement les problèmes au quotidien.
Ainsi, on ne gaspille pas de temps et d'énergie dans une analyse approfondie inutile, qui au mieux n'apportera rien de plus, et, au pire, génèrera des contraintes ou des coûts supplémentaires qui auraient pu être évités.
Certain(e)s parmi vous auront perçu, au travers de ces questions du "filtre", l'importance de l'audit qui a été décrit précédemment.
L'audit joue bien ici un rôle préventif en s'assurant que les Standards de travail sont connus, compris, adaptés et appliqués.
Il contribue donc à éviter la survenue d'un certain nombre de problèmes.
Conclusion
Le Travail Standard constitue une des bases du déploiement du Lean Management.
Sans sa mise en application, il sera impossible de mener une démarche de progrès permettant d'atteindre des objectifs ambitieux en Qualité, Coûts et Délais.
A l'inverse, la mise en oeuvre, sous l'impulsion de la Direction, ce principe va permettre de réunir un certain nombre de conditions nécessaires à l'amélioration de la performance.