Le Juste-A-Temps (JAT) est un principe qui consiste à réaliser une opération de façon à ce qu'elle produise son résultat uniquement au moment où il est nécessaire ("juste à temps").
Il constitue un des deux piliers du "temple" du Lean et donc du système de production mis en place par Toyota.
C'est ce principe qui régit le fonctionnement du flux tiré. Il peut s'appliquer aussi bien à une succession d'opérations de production qu'à des opérations de traitement d'informations.
Nous allons voir dans un premier temps les principes fondamentaux du JAT.
Nous balayerons ensuite les étapes nécessaires à mise en place.
Puis, nous évoquerons quelques avantages et inconvénients de cette méthode.
JAT : définition
Le Juste-à-Temps (JAT) est une méthode de gestion de production qui vise à produire les quantités nécessaires de produits au moment précis où elles sont demandées par les clients, sans avoir de stocks excessifs de matières premières, de composants ou de produits finis.
Cette approche étroitement liée à la planification et à l'ordonnancement de la production, nécessite une synchronisation précise des activités de fabrication avec les besoins réels, minimisant ainsi les stocks et favorisant une gestion fluide des processus de production.
Le JAT peut aider à réduire les temps de cycle dans la chaine de valeur, ce qui permet de produire des produits de manière plus rapide et plus efficace.
Les principes du Juste-à-Temps
Pour atteindre son objectif, le Juste-à-Temps s'appuie en particulier sur les deux principes suivants :
1) Tendre vers la suppression des stocks intermédiaires
Dans une organisation telle qu'une entreprise, toute activité consiste en une succession de différentes étapes.
Ces étapes successives peuvent être réalisées par une ou plusieurs personnes, et sur une ou plusieurs machines.
Par exemple, en production, il peut y avoir une étape A qui consiste à usiner une pièce mécanique, puis une étape B qui consiste à peindre cette pièce.
Ou pour une visite médicale, une étape A qui consiste à la réalisation d'examens par un infirmier, puis une étape B avec un diagnostic par un médecin.
Le Juste-à-Temps consiste à enchaîner directement les étapes A et B, sans qu'il n'y ait un stock de pièces ou des patients qui soient en attente entre les deux étapes.
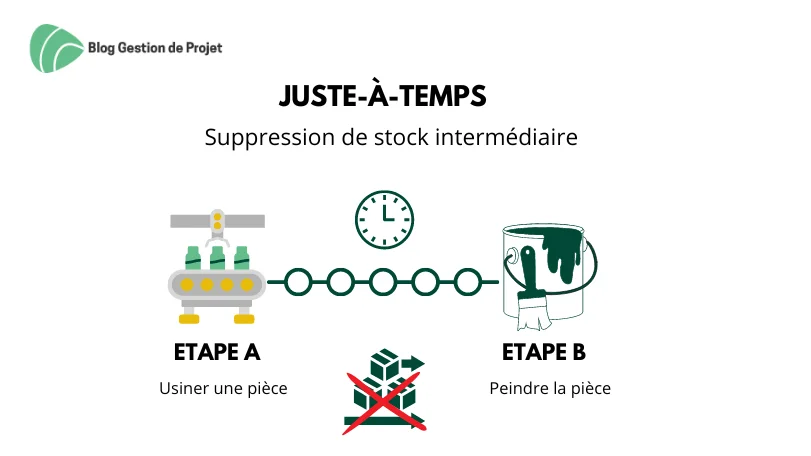
2) Produire juste la quantité demandée au moment où elle est demandée
Il y a donc dans le Juste-à-Temps une notion de cadencement et de synchronisation de la demande.
Le travail doit être organisé de manière à ce qu'une étape produise ou fournisse exactement ce qui est demandé par l'étape suivante, dans la bonne quantité (ni plus ni moins), et au bon moment.
Comment mettre en place le Juste-à-Temps ?
Il faut avoir conscience que la mise en place du Juste-à-Temps est un chantier conséquent avec de multiples "tiroirs". C'est une démarche qui prend du temps et qui nécessite d'aller au fond des choses.
En voici les principales étapes, qui sont à adapter au contexte de chaque entreprise :
1) Inclure les personnes du terrain dans la démarche
Comme pour la plupart des actions menées dans le cadre d'une démarche Lean, la mise en place du Juste-à-Temps va constituer un changement qui peut être radical dans l'organisation du travail.
Pour s'assurer de faire les bons choix lors du déploiement du Juste-à-Temps et pour accompagner au mieux ce changement, il est crucial d'impliquer les personnes concernées le plus en amont possible dans la démarche.
Pour cela, la matrice RACI permet d'affecter les rôles et responsabilités de manière claire et transparente.
2) Analyser le flux avec une VSM
Le Juste-à-Temps est un principe du flux tiré.
Il s'applique à une succession d'opérations, c'est-à-dire un flux. Le premier outil Lean indispensable pour une première approche du flux concerné est l'analyse à l'aide d'une Value Stream Mapping (VSM).
Cette dernière servira de base pour mener les étapes suivantes.
3) Déterminer le temps de takt
Nous l'avons vu plus haut, le Juste-à-Temps consiste à effectuer une opération "au bon moment".
Pour déterminer la cadence de production qui va correspondre à la demande des clients, c'est le Temps de Takt qu'il est nécessaire de déterminer.
4) Rechercher les sources de gaspillages (Mudas)
Pour pouvoir enchaîner chaque opération au bon moment, il est important d'identifier les éléments qui peuvent nuire à l'efficacité du flux.
Pour cela, nous procédons à la recherche des sources de gaspillages, connues sous le nom de Mudas dans le domaine du Lean.
Ces Mudas peuvent être classifiés en 7 catégories, parmi lesquelles on trouve la production de défauts, l'attente des opérateurs ou encore la génération de stocks intermédiaires.
Une fois ces sources de gaspillages identifiées, il convient évidemment de travailler à leur suppression.
5) Mettre en place des standards
Afin d'assurer le déroulement régulier des opérations dans le cadre d'une organisation en Juste-à-Temps, il est important d'établir les standards de travail qui vont permettre une bonne répétitivité et une bonne répétabilité de la réalisation des tâches.
Ces standards serviront également de support pour procéder à l'équilibrage des postes de travail, c'est-à-dire répartir de façon homogène la charge de travail entre les opérateurs.
Cette répartition s'appuie nécessairement sur le temps de takt.
Supposons par exemple que la réalisation d'une pièce nécessite 4 opérations manuelles successives d'une durée de 48 secondes chacune.
Si le temps de takt est proche des 48 secondes (c'est-à-dire que les clients attendent en moyenne la livraison d'une pièce toutes les 48 secondes), alors le standard va prévoir 4 opérateurs, chacun en charge d'une des quatre opérations.
Si par contre le temps de takt est plus proche des 100 secondes, alors le standard prévoira 2 opérateurs, l'un en charge de réaliser successivement les deux premières opérations (ce qui lui prendra environ 96 secondes), l'autre en charge de réaliser les 3ème et 4ème opérations.
Enfin, ces standards serviront de base à l'amélioration continue de ces opérations.
6) Analyser la variabilité et dimensionner des stocks tampons
Une organisation en Juste-à-Temps "idéale" avec la suppression totale de tous les stocks intermédiaires va forcément être impactée par le moindre petit écart rencontré sur le flux : par exemple un défaut généré sur le produit lors d'une étape, une rupture de livraison ou encore une panne sur une machine.
Pour absorber ces aléas, il faut dans un premier temps les identifier et les quantifier.
Cela peut se faire en analysant des historiques et/ou en observant la production sur une période suffisamment longue et représentative.
Ces aléas constituent ce que l'on appelle la "variabilité". Lorsqu'elle est quantifiée, cela permet de mettre en place, à certaines étapes du flux, des stocks tampons qui permettront d'absorber les aléas.
Par exemple, un stock tampon correspondant à 15 minutes de production positionné juste avant un poste de travail permettra de neutraliser les effets d'une panne de durée inférieure ou égale à 15 minutes survenant en amont dans le flux.
Les stocks tampons se disposent principalement juste avant les postes de travail "goulots".
Bien évidemment, puisque le Juste-à-Temps tend à aller vers le "zéro stock", ces stocks tampons doivent être dimensionnés au juste nécessaire.
Et ils doivent régulièrement être challengés et réduits suite à des chantiers d'optimisation tels que de la TPM (Total Productive Maintenance, c'est-à-dire de la fiabilisation des équipements), du SMED (diminution des temps de changement de série), ou encore des dispositifs type poka-yoke (détrompeurs) qui évitent la génération de défauts sur ce qui est produit.
7) Interface avec les clients et fournisseurs
La plupart du temps, un flux de production ou d'informations dépend en amont de matières premières ou d'informations provenant de l'extérieur, et va générer un produit ou un service qui sera transmis également vers un client extérieur.
Ainsi, une démarche de Juste-à-Temps va à un moment donné nécessiter d'organiser le flux dans son ensemble et de travailler sur les interfaces avec nos fournisseurs en amont et avec nos clients en aval, c'est donc un
flux généré par le client.Avantages et inconvénients du Juste-à-Temps
De nos jours, il y a un consensus dans la plupart des entreprises sur les bénéfices apportés par la mise en place du Juste-à-Temps.
Il faut également être conscient des impacts plus négatifs et de la façon de les minimiser.
Passons en revue les principaux avantages et inconvénients :

1) Avantages du juste-à-temps
Les avantages du juste-à-temps sont :
- Une diminution du temps d'écoulement nécessaire pour la réalisation de l'ensemble des opérations
- Un gain d'espace et de manutention
- Une diminution des rebuts
1.1 Diminution du temps d'écoulement nécessaire pour la réalisation de l'ensemble des opérations
Cela correspond au temps entre la réception de la demande du client et la livraison du produit ou service demandé.
Le Juste-à-Temps implique donc un meilleur temps de réponse et une meilleure réactivité qui devraient améliorer la satisfaction des clients.
Cette "compression" du temps entre le lancement de la production et la livraison permet également de diminuer le temps entre le moment où l'entreprise engage des dépenses (énergie, salaires, nécessaires pour produire) et le moment où elle collecte ses recettes (facturation du client à la réception).
Ainsi, le Juste-à-Temps induit aussi une amélioration de la trésorerie de l'entreprise qui peut être assez significative.
1.2 Gain d'espace et de manutention
En diminuant les stocks intermédiaires, le Juste-à-Temps peut réduire significativement le besoin de place nécessaire pour le stockage.
Conséquemment, il y aura des gains financiers liés à la fois au moindre besoin d'acquisition ou de location de surface de stockage, et à la diminution des opérations de manutention nécessaires pour les mouvements vers et depuis le stock.
1.3 Diminution des rebuts
En limitant les stocks intermédiaires, si des défauts commencent à être générés suite, par exemple, à un déréglage ou à une autre défaillance technique, ils vont être détectés plus rapidement puisque les produits défaillants vont passer directement et rapidement à l'étape suivante.
Cela évite d'accumuler des défauts dans un stock intermédiaire sans s'en rendre compte et de devoir ensuite rebuter ou reprendre un grand nombre de pièces.
2) Inconvénients du juste-à-temps
Les inconvénients du juste-à-temps sont :
- Une forte sensibilité à la moindre variabilité
- Un impact sur les modes de transport
2.1 Forte sensibilité à la moindre variabilité
Nous l'avons vu plus haut : la configuration idéale du Juste-à-Temps consiste à supprimer intégralement tous les stocks intermédiaires. Ce qui expose le flux à un arrêt dès la survenance du moindre aléa.
Il convient donc :
- De travailler sur la réduction de la variabilité, dans le cadre de chantier Lean
- Et en attendant, de compenser cette variabilité par des stocks tampons là où c'est nécessaire, stocks tampons dont le dimensionnement devra être réduit progressivement au fur et à mesure des progrès.
2.2 Impact sur les modes de transport
La diminution et a fortiori la suppression des stocks intermédiaires engendrés par le Juste-à-Temps impliquent de devoir transporter beaucoup plus souvent des petites quantités de produits d'un poste de travail au suivant (par opposition avec des regroupements de transports lorsque l'on n'est pas dans une démarche Juste-à-Temps).
Si certaines étapes de fabrication doivent être réalisées sur un site différent et distant géographiquement, nous chercherons donc à affréter très régulièrement des petits transports.
Cela peut vouloir dire par exemple d'envoyer des camions unitaires plutôt que de pouvoir faire des regroupements par trains. D'où des coûts de transport plus élevés et un potentiel impact environnemental.
Ces aspects nécessitent, eux aussi, une réflexion pour pouvoir imaginer des solutions nouvelles adaptées au Juste-à-Temps et au contexte de l'entreprise.
Il pourrait s'agir par exemple de l'acquisition d'une petite fourgonnette électrique de taille adaptée à la quantité à transporter.
Conclusion
Le Juste-à-Temps est un principe d'optimisation des flux de production ou d'information qui peut amener des gains significatifs dans les domaines de la qualité, des délais et des coûts.
Mais sa mise en œuvre nécessite un travail global et de longue haleine afin de traiter tous les aspects qui vont contribuer à la baisse de la variabilité sur le périmètre que l'on veut organiser en Juste-à-Temps.
"Conviction" et "persévérance" font partie des maîtres-mots pour une telle implantation.
C'est pourquoi le Juste-à-Temps va forcément s'inscrire dans une démarche Lean, globale, portée par la Direction de l'entreprise, et nécessitant l'implication de tous.