Une VSM, acronyme de Value Stream Mapping, est une représentation d'un processus qui permet de distinguer les étapes qui représentent une valeur ajoutée pour le Client, et celles qui n'apportent pas de valeur ajoutée au produit ou service fourni.
C'est un outil incontournable d'une démarche Lean.
Nous verrons dans cet article les fondamentaux d'une VSM :
Comment l'établir et exploiter les résultats de celle-ci, ainsi que ses avantages et limites.
Pourquoi faire une VSM ?
VSM signifie "Value Stream Mapping", que l'on peut traduire littéralement par "cartographie de la chaîne de valeur" ou analyse des flux de production.
Elle découle du principe des flux tirés.
Utilisé dans le Lean Management, cette analyse des flux est utilisée dans le but :
- D'établir un diagnostic de l'efficacité d'un flux et mettre en avant les axes d'amélioration qui seront repris dans les objectifs de l'organisation ou de l'entreprise
- De servir de support à un recensement des sources de gaspillages (ou "non-valeurs-ajoutées") à chaque étape du processus analysé, gaspillages qui pourront faire l'objet de chantiers d'amélioration.
VSM : Définition
Il s'agit d'une cartographie du flux de la valeur qui sert à classer les étapes du flux analysé en quatre catégories, dans le but de représenter visuellement un processus en permettant de distinguer les valeurs ajoutées par rapport aux gaspillages.
Voici les 4 catégories inhérentes à ce concept :
- Les étapes de TRANSFORMATION, durant lesquelles le produit ou service est modifié, représentées par un rond vert
- Les étapes de CONTRÔLE, durant lesquelles aucune transformation n'a lieu, mais où l'on vérifie la qualité du produit ou service ; ces étapes sont représentées par un carré bleu
- Les étapes de TRANSPORT, représentées par une flèche jaune
- Et les étapes de STOCKAGE, lorsqu'aucune opération ni aucun déplacement ne se produit, représentées par un triangle inversé rouge.
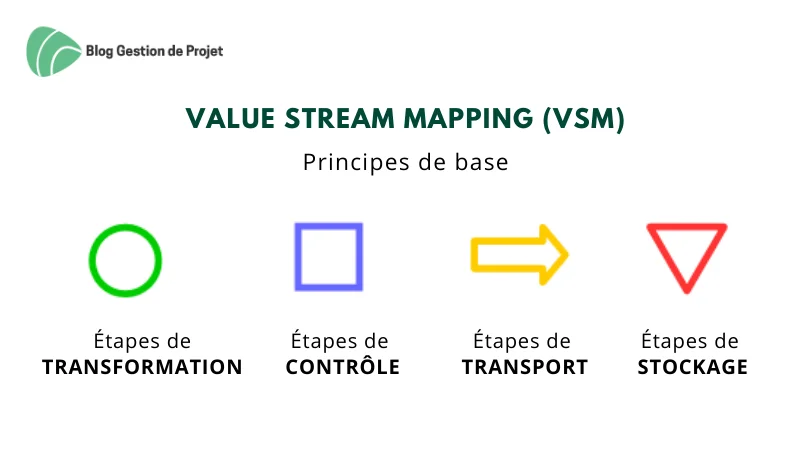
Voyons ces catégories de plus près :
La seule catégorie qui représente une valeur ajoutée pour laquelle le Client est prêt à payer est la TRANSFORMATION.
Il s'agit par exemple de la découpe d'une planche de bois qui va servir à fabriquer une étagère qu'un Client achètera.
Ou encore de l'affectation d'une chambre d'hôtel avec vue sur la mer à la réservation d'un Client qui vient d'exprimer une telle demande.
De manière intuitive, on comprend bien que le TRANSPORT d'un produit ou son STOCKAGE n'apportent aucune valeur ajoutée au produit.
Le CONTRÔLE porte davantage à confusion.
Dans la grande majorité des cas, on considère qu'il ne s'agit pas non plus d'une opération à valeur ajoutée.
En effet, si notre processus est tellement peu fiable qu'il nous faut ajouter trois personnes à la fin d'une ligne de fabrication pour recontrôler tous les articles, le Client ne va pas accepter de financer ce surcoût.
VSM : Exemple
Voici un modèle VSM Excel à télécharger.
Il s'agit d'un exemple de feuille de relevés ou fiche de collecte de données qui permet de noter les observations faites sur le terrain.
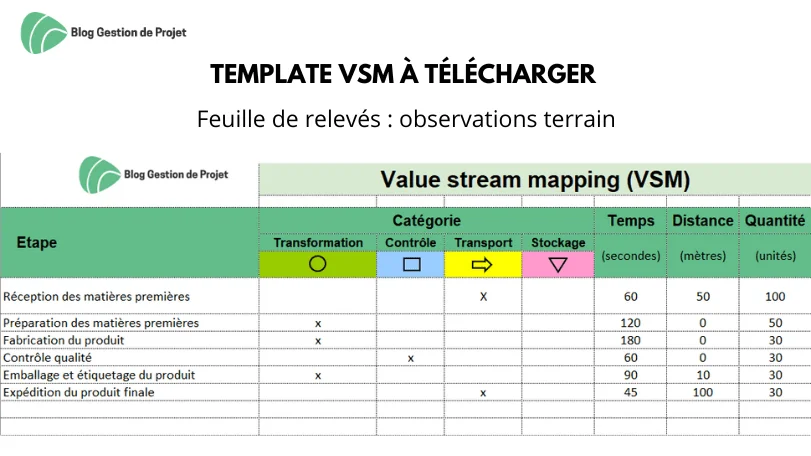
Comment faire une VSM ?
La réalisation d'un outil VSM se déroule en 3 étapes :
- Étape 1 - Observation terrain : observer et récolter des informations sur le flux
- Étape 2 - Représentation visuelle : le groupe de travail va représenter visuellement la cartographie de la chaine de valeur
- Étape 3 - Calculs : quelques calculs vont donner des indications complémentaires sur la « performance » du flux.
Découvrons plus en détails ces 3 étapes.
1) Observation terrain et collecte d'information
Rappelons ici que le flux analysé peut être un flux physique, lié à la fabrication d'un article, ou bien un flux de données, lié à la réalisation d'un service ou à la fourniture d'informations.
1.1) Les questions à se poser
Avant d'aller observer sur le terrain, il est nécessaire de valider deux points importants :
Qu'est-ce que l'on veut suivre ?
Ici, il faut préciser l' « objet » dont on veut suivre le flux.
Par exemple une pièce mécanique qui va être transportée et transformée tout au long d'une ligne de production.
Ou bien une commande client qui peut arriver sous forme d'un e-mail et qui va être transformée en ordre de fabrication par les équipes commerciales et ordonnancement.
Ce que l'on suit doit forcément correspondre au produit et/ou service que l'on vend au Client.
Une cartographie VSM ne consiste pas à représenter les étapes successives du travail d'un opérateur, mais bien à suivre la transformation de ce qui est vendu au Client.
Quels sont le point de départ et le point d'arrivée du flux à représenter ?
Pour éviter les hésitations une fois sur le terrain, il convient de définir clairement à l'avance où commence et où s'arrête le flux que l'on veut analyser.
Il n'y a pas ici de bonne ou de mauvaise réponse : c'est un choix que l'on fait, un périmètre que l'on définit.
Par exemple, dans une usine de fabrication de papier vendu sous forme de ramettes A4, on peut choisir d'analyser le flux à partir de la bobine de papier.
Celle-ci se déroule en début de machine, jusqu'à l'emballage d'une ramette.
Ou bien à partir du tronc d'arbre qui constitue la matière première, jusqu'au chargement de la palette de cartons remplis de ramettes sur le camion... ce qui prend évidemment plus de temps à traiter.
Une fois que des réponses précises ont été apportées à ces deux questions, elles doivent être notées par l'équipe d'observateurs, car cela va cadrer tout leur travail sur le terrain.
1.2) Les données à collecter
L'observation terrain va consister à suivre en détails le flux du produit ou service sélectionné.
Chaque étape devra être identifiée et décrite.
La première information à collecter pour chaque étape est sa nature, parmi les 4 catégories utilisées pour une analyse VSM :
- Transformation
- Contrôle
- Transport
- Stock
Ensuite, d'autres informations sont à mesurer à chaque étape :
- La quantité de produits en cours de transformation, de contrôle, de transport ou stockés
- Le temps de cycle, c'est-à-dire la durée nécessaire à la transformation ou au contrôle d'une unité. Et ce, uniquement pour les étapes de transformation et de contrôle
- La distance parcourue, et ce, uniquement pour les étapes de transport
1.3) Sur le terrain
Pour aller réaliser l'observation terrain sur un flux, l'équipe-type idéale est composée de 3 à 5 personnes :
- 1 ou 2 experts du flux qui vont pouvoir expliquer précisément ce qu'il se passe à chaque étape
- 1 ou 2 personnes en charge de la mesure des temps de cycle, des distances et des quantités en cours
- 1 personne, de préférence non-experte du flux, chargée de prendre les notes sur la feuille de relevés
Si l'on dispose d'une équipe de plus de 5 personnes, il est possible d'analyser plusieurs flux en parallèle, par exemple plusieurs lignes de production, ou bien de scinder le flux en plusieurs parties pour se répartir le travail.
2) Représentation visuelle du flux
Après observation et collecte d'information, vient l'étape de la représentation visuelle des flux.
Voici les étapes à suivre pour représenter le flux d'informations :
2.1) Représenter les étapes du flux à l'aide de post-its
Une fois de retour en salle, je vous suggère d'utiliser un mur ou un grand rouleau de papier sur lequel on va représenter les étapes du flux à l'aide de post-its. Traditionnellement, on utilise des post-its de :
- couleur verte pour les étapes de transformation,
- bleue pour les étapes de contrôles,
- jaune pour les étapes de transport,
- et rouge/rose pour les étapes de stockage.
2.2) Positionner les post-it dans l'ordre des étapes
Les post-its de la couleur appropriée sont positionnés sur la feuille dans l'ordre des étapes du flux.
Pour une meilleure visualisation, on reprend sur chaque post-it le symbole de la catégorie correspondante (rond pour la transformation, carré pour le contrôle, etc.) et le titre de l'étape.
2.3) Correspondre les données collectées aux étapes
En dessous de chaque post-it, on recopie les données relevées à chaque étape : quantité, temps de cycle et/ou distance.
Voici un exemple de la VSM représentée visuellement pour permettre l'analyse des flux :
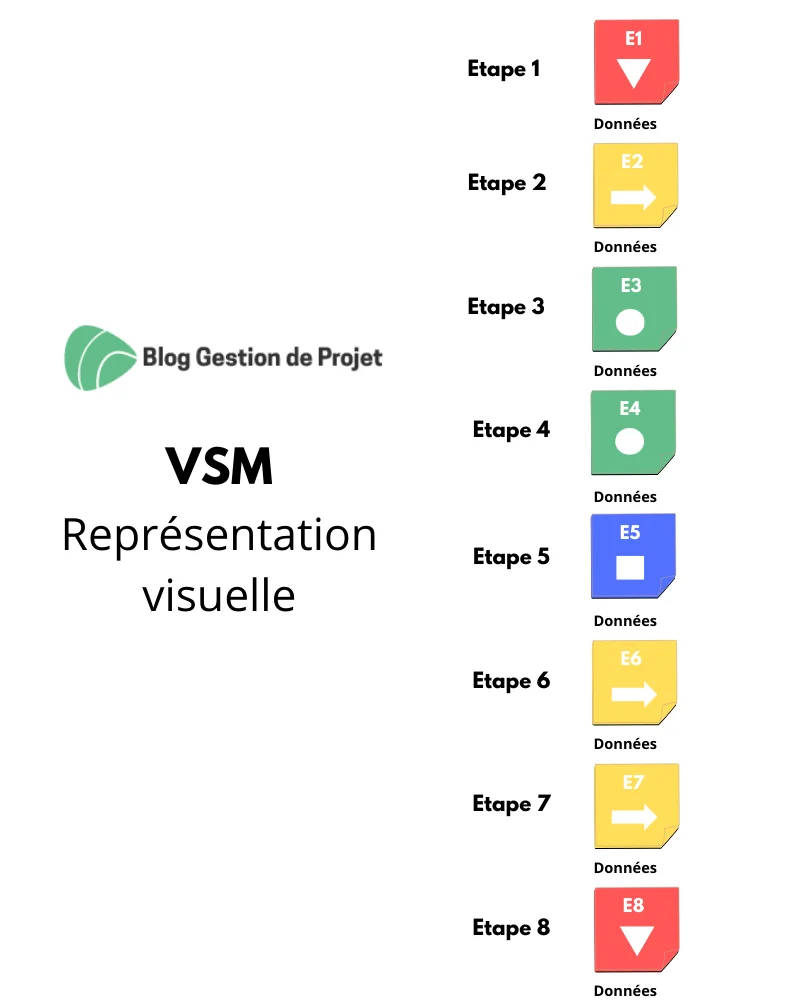
3) Quelques unités de calculs indispensables
En complément de la représentation visuelle du flux, les données récoltées durant l'observation permettent de faire quelques analyses complémentaires.
Voici quelques premiers calculs à effectuer :
- Temps total de transformation : obtenu en additionnant les temps de cycle de chaque étape de transformation
- Temps total de contrôle : obtenu en additionnant les temps de cycle de chaque étape de contrôle
- Distance totale : obtenue en additionnant les distances de chaque étape de transport
- Quantité totale en en-cours dans le flux : obtenue en additionnant les quantités observées à chaque étape
À ce stade, il est déjà utile de s'interroger sur la "distance totale".
Le fait de transporter un produit n'est pas une valeur ajoutée. Certains sites de production non optimisés font parcourir des kilomètres inutiles à leurs produits fabriqués.
Voici d'autres indicateurs importants :
- Le temps d'écoulement du flux ou Lead time
- Le temps de Takt
- Le ratio "temps total de transformation / Temps d'écoulement"
Voyons chacun de plus près :
3.1) Le temps d'écoulement du flux ou Lead time
Le "temps d'écoulement" du flux, "lead time" en anglais, correspond au temps qui s'écoule entre l'arrivée d'un nouveau produit ou service en entrée de flux et sa sortie en fin de flux.
Sur des flux longs avec un certain nombre d'étapes de stockage, le "temps d'écoulement" peut être calculé à partir du "temps de takt".
3.2) Le temps de takt
Le temps de takt correspond au rythme de la demande client et s'exprime comme la périodicité à laquelle il faut produire chaque unité pour satisfaire exactement la demande.
Par exemple, si un site fonctionne 8 heures par jour du lundi au vendredi et que les clients commandent en moyenne 400 produits par semaine, alors le « temps de takt » est égal à (8 heures x 5 jours / 400) = 6 minutes.
Il est possible de calculer le "temps d'écoulement" en multipliant le "temps de takt" par la "quantité totale en en-cours dans le flux".
Ce temps d'écoulement est très intéressant du point de vue du Client.
S'il est calculé sur un flux complet analysé depuis la réception de la demande du Client jusqu'à la livraison du produit ou du service demandé, il correspond alors au délai d'attente du Client après qu'il a passé sa commande pour la recevoir.
C'est potentiellement un indicateur stratégique sur lequel une entreprise va vouloir améliorer sa performance.
3.3) Le ratio "temps total de transformation / Temps d'écoulement"
Enfin, il est intéressant de calculer le ratio du "temps total de transformation" divisé par le "temps d'écoulement".
Cela représente la proportion de valeur ajoutée en temps sur l'ensemble du flux.
Sur des flux de production complexes, il n'est souvent que de quelques pourcents.
Voici en infographie les indicateurs clés résumés :
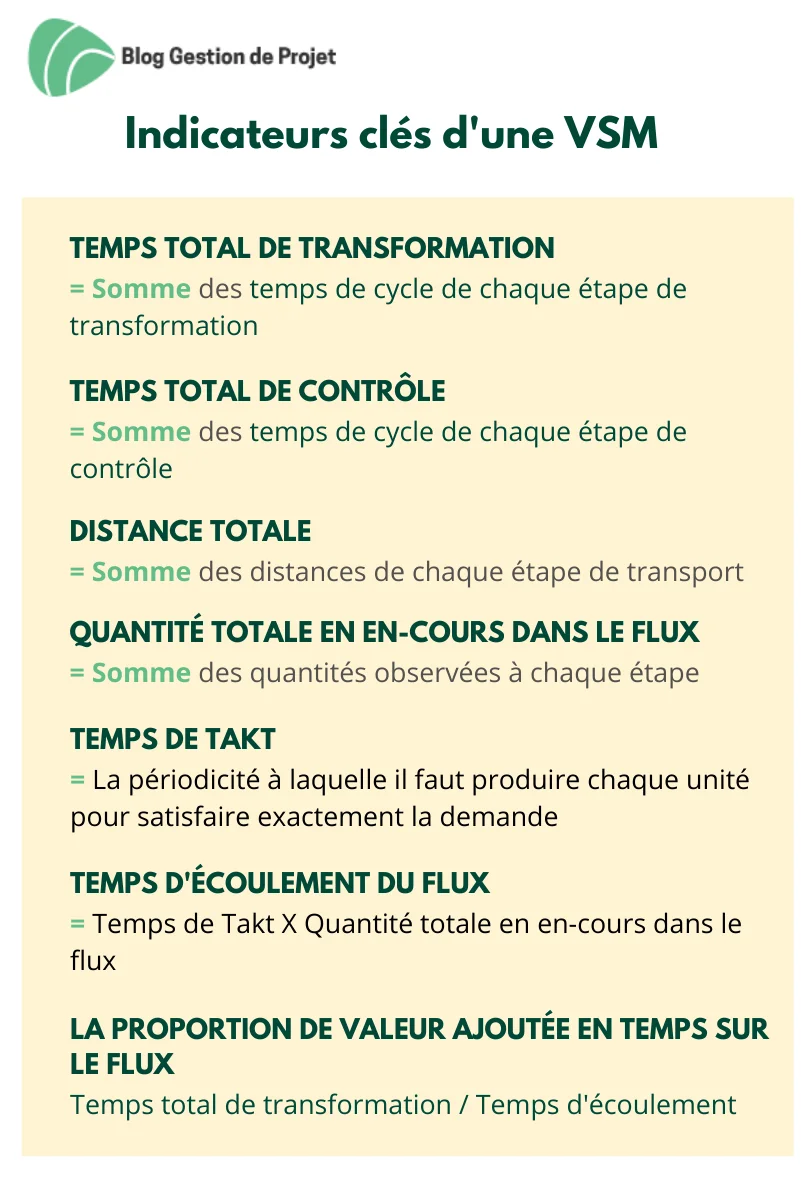
Comment exploiter les résultats d'une VSM
La cartographie représente la situation actuelle des flux analysés.
Elle met en évidence un certain nombre de gaspillages.
Voici comment exploiter les résultats :
1) Définir les axes d'amélioration à intégrer dans la démarche Lean
L'observation de la représentation du flux permet à un Comité de Direction de déterminer une partie de sa démarche Lean en établissant les axes d'améliorations sur lesquels travailler.
Il est possible d'utiliser la même représentation visuelle que la Value Stream Mapping pour représenter le flux « cible », fictif pour le moment, mais qui intègre les simplifications que l'entreprise prévoit de réaliser.
2) Définir les chantiers d'amélioration pour déployer la démarche Lean
La cartographie des flux des données actuelle peut aussi servir de support pour que le Comité de Direction indique, à chaque étape du processus, les chantiers d'amélioration qui seront nécessaires pour déployer la stratégie et qui devront être reportés sur la feuille de route.
Voici quelques exemples de chantiers d'amélioration qui peuvent cibler certaines étapes d'un processus :
- Améliorer le temps de changement de commande sur une machine de production (démarche « SMED »)
- Supprimer une étape de stockage de produits semi-finis sous-traitée dans des entrepôts extérieurs loués
- Améliorer la performance d'un équipement par une démarche TPM et l'analyse du TRS
- Améliorer la cadence d'une machine qui est goulot dans le flux
- Améliorer la performance énergétique d'une installation
- Fiabiliser un process de façon à pouvoir supprimer une étape de contrôle
Avantages et limites
Pour utiliser l'outil d'analyse des flux à bon escient, il est important d'être conscient de ce qu'il apporte et de ses limites.
1) Avantages
Au-delà de l'intérêt fondamental de la Value Stream Mapping pour réaliser des diagnostics afin d'élaborer une démarche Lean, l'outil présente un certain nombre d'atouts :
- C'est un outil très visuel, particulièrement adapté pour analyser un flux dans le cadre d'un groupe de travail
- L'équipe qui va réaliser l'observation du flux sur le terrain et effectuer sa représentation va acquérir et partager une connaissance fine du processus analysé. La démarche est très formatrice, en particulier pour les personnes qui sont moins familières avec le flux
- Très souvent, les résultats mis en avant par l'outil sont surprenants, même pour les experts qui travaillent au quotidien sur le flux analysé. Il permet des prises de conscience sur un certain nombre de sources d'inefficacité
2) Limites
Une cartographie de la chaine de valeur est une photographie d'un processus à un moment donné.
Les résultats, notamment les temps de cycles et les quantités en en-cours peuvent être très différents entre deux VSM d'un même processus réalisé à des moments distincts.
Bien qu'une représentation des flux permette de mettre en avant certains gaspillages sur lesquels il sera éventuellement possible de travailler (les contrôles, les transports et les stocks), elle ne fait pas apparaître l'ensemble des gaspillages connus comme les « 7 mudas » du Lean.
Les déplacements des opérateurs, l'attente des opérateurs, les rebuts, la surproduction et certains process inutiles ne sont pas mis en évidence par cet outil.
3) Points de viligance
Il est assez fréquent que des étapes du processus soient oubliées lors des observations sur le terrain.
Pour limiter ce risque, une astuce consiste à suivre le flux à observer non pas dans le sens du flux, mais dans le sens inverse.
Cela force à se poser davantage de questions.
Certaines périodes ne sont pas adaptées pour réaliser la représentation des flux.
Par exemple durant une panne sur une ligne de production.
Le fait que la ligne soit arrêtée va fausser les mesures d'en-cours, rendre impossible les mesures de temps de cycle et le risque d'oublier une étape sera plus élevé.
Conclusion
La VSM sera forcément indispensable à un moment au cours du démarrage et/ou du déploiement d'une démarche Lean.
Elle permet de représenter de façon relativement simple un flux, tout en mettant en avant un certain nombre de pistes d'amélioration.