Dans les environnements industriels, les chaînes d’approvisionnement représentent un enjeu important pour la performance de l’entreprise. Et dans le cadre des démarches d’excellence opérationnelle qui s’appuient sur le Lean, une grande partie de l’amélioration concerne l’analyse et l’optimisation des flux. Il est ici question à la fois des flux internes à l’entreprise et des flux globaux auxquels elle fait partie.
Cet article décrit à quoi ressemble le fonctionnement idéal d’une chaîne d’approvisionnement. Nous analyserons également les principales difficultés à cette optimisation, et nous verrons les pistes d’actions qui permettent de se rapprocher d’un flux d’approvisionnement idéal.
Qu’est-ce qu’une chaine d’approvisionnement ?
Une chaîne d'approvisionnement est l'ensemble des étapes successives qui permettent d'acheminer et de transformer des matières premières en produits nécessaires et commandés par une entreprise.
Elle requiert fondamentalement une planification et un ordonnancement efficaces de la production pour maintenir sa fluidité, sa réactivité et sa capacité à répondre efficacement aux besoins changeants du marché.
Le fonctionnement idéal d'une chaîne d'approvisionnement
Dans le domaine des approvisionnements, imaginons un instant le contexte idéal : à tout moment, vous avez à disposition le matériel et les consommables nécessaires, et uniquement le matériel et les consommables nécessaires, sans stock inutile, conformément aux principes du Juste À Temps.
Certaines entreprises fonctionnent déjà de manière très proche de cet idéal, notamment les constructeurs automobiles avec leurs équipementiers.
Regardons les éléments qui caractérisent un tel scénario d'approvisionnement idéal :
1. Étalement des livraisons au fil des besoins
L'approvisionnement idéal consiste à recevoir chaque composant au fur et à mesure des besoins. Cela peut se traduire par une livraison par jour, avec précisément la quantité qui va être utilisée durant cette période, voire plusieurs livraisons dans la journée.
Cette configuration est évidemment facilitée par une proximité géographique entre le fournisseur et le client, ce qui va réduire le délai de livraison ainsi que le risque d'aléa lié au transport.
Cela demande que le fournisseur fonctionne selon les principes du Juste À Temps et du Flux Tiré. C'est-à-dire notamment qu'il produise uniquement en mode "pièce à pièce" les quantités demandées, et qu'il ne fabrique pas par lots de centaines ou de milliers de pièces à la fois.
Le fournisseur doit livrer les pièces en faisant appel à des transports plus fréquents, mais de plus faible capacité. En effet, s'il voulait viser des économies sur volume en regroupant des quantités importantes sur un seul "gros" transport, nous perdrions tout l'intérêt de la production en pièce à pièce.
Pour éviter les accumulations de stocks, que ce soit chez le fournisseur ou chez le client, il est également nécessaire de synchroniser les jours et les heures d'ouverture entre les deux entreprises.
En effet, si le client travaille 7 jours sur 7 et 24 heures sur 24, alors que le fournisseur travaillerait exclusivement de 8h à 18h du lundi au vendredi, cela impliquerait nécessairement une génération de stocks pour répondre aux besoins permanents du client.
2. Qualité totale et élimination en amont des défauts
La conformité aux normes de qualité ainsi que la réduction des défauts sont des facteurs clés de succès d'une chaine d'approvisionnement.
Avec des approvisionnements ainsi livrés "Juste À Temps" et avec uniquement la quantité nécessaire, il est impératif que chaque élément fourni soit utilisable. Cela nécessite donc une absence de défauts, soit 100% de la quantité livrée conforme.
Pour atteindre ce résultat, il est probable que le fournisseur ait à mettre en place une démarche de Qualité Totale.
Pour s'assurer qu'aucun défaut n'arrive chez le client, le système qualité du fournisseur doit pouvoir les identifier et les intercepter en interne. Un outil idéal pour cela est l'utilisation de poka-yoke. Il s'agit de systèmes anti-erreur qui, par conception, empêchent les défauts d'être générés, indépendamment de l'application de procédures ou d'autres facteurs humains.
À défaut de poka-yoke, le fournisseur peut également mettre en place un "mur qualité", c'est-à-dire un dispositif d'inspections poussées. Mais dans ce cas, nous nous éloignons déjà du scénario idéal puisqu'un mur qualité nécessite des ressources supplémentaires et est donc coûteux.
3. Flexibilité et connaissance des besoins clients en temps réel
Pour respecter la logique du Juste À Temps, les flux du client et du fournisseur doivent être liés.
Ainsi, si un incident stoppe la production chez le client, le fournisseur doit en être informé immédiatement pour arrêter sa propre production et éviter de générer du stock.
Il existe dans certaines entreprises des systèmes d'affichage visuels, avec des indications de quantités et également des voyants vert / jaune / rouge, qui informent le fournisseur en temps réel de l'état de la production chez le client et des besoins d'approvisionnement immédiats.
Les principaux freins à l'optimisation de la chaine d'approvisionnement
La réalité peut souvent différer et même avec une forte volonté de l'entreprise, il peut être difficile de fiabiliser l'ensemble du flux d'approvisionnement.
Voyons quelles sont les difficultés rencontrées le plus fréquemment :
1. Différentes sources de variabilité
Il peut exister une multitude de sources de variabilité.
Un exemple peut être le manque de fiabilité des équipements de production.
Si de nombreuses pannes et/ou des pannes de longue durée se produisent, alors le temps de disponibilité des équipements de production pourra être très variable d'un jour à l'autre, voire d'une semaine à l'autre, avec comme conséquence directe une variabilité dans les quantités produites et vendables aux clients.
Un autre exemple, sur des process de production manuels, peut être une forte différence de temps de cycle, c'est-à-dire le temps nécessaire pour fabriquer une pièce, d'un opérateur à un autre.
Cela peut être dû à un manque de formation, ou à des périodes avec la présence de nombreux travailleurs intérimaires, ou encore à un manque de standardisation.
2. Des périodes de fermeture de sites
Selon le type d'industrie et la taille de l'entreprise, il est fréquent que certains sites soient totalement fermés durant des périodes de congés, par exemple en France une semaine en fin d'année et trois à quatre semaines durant l'été.
Si un tel site approvisionne une industrie qui fonctionne 365 jours par an, il va forcément y avoir une rupture dans la régularité de l'approvisionnement :
- Dans le meilleur des cas, si c'est anticipé, cela va générer un pic de production qui peut être difficile à absorber chez le fournisseur, ainsi que la constitution d'un stock chez le client
- Dans le pire des cas, il pourra y avoir une rupture de stock et un arrêt de production chez le client.
3. Un taux de défauts trop élevé
Si le nombre de produits défectueux est important, et même si le fournisseur est capable de garantir une régularité dans sa fabrication de pièces, c'est le nombre de pièces bonnes fournies qui ne pourra pas être maîtrisé.
Ici aussi, les conséquences seront soit la constitution d'un stock chez le client, soit le risque de rupture et d'arrêt de production.
Découvrez ici comment anticiper et évaluer les défaillances.
4. L'effet coup de fouet
L'effet coup de fouet peut être responsable à la fois d'une forte génération de stock, et aussi à l'inverse de la survenue de ruptures.
Il se produit au niveau d'une chaîne d'approvisionnement constituée de plusieurs intermédiaires et lorsqu'il y a un manque de visibilité sur les quantités demandées par le client final.
Exemple :
Si un client final commande ponctuellement une quantité plus élevée d'un produit à son distributeur, celui-ci va y répondre en piochant dans son stock de sécurité.
Ensuite, ce distributeur va commander à son grossiste une quantité encore plus importante pour réapprovisionner la quantité vendue, pour reconstituer un stock de sécurité, voire également pour anticiper une tendance à la hausse de la demande (alors que cette tendance n'est peut-être pas pérenne).
Ainsi une demande ponctuellement multipliée par un facteur x2 du client au distributeur, peut générer une quantité commandée de x3 ou x4 du distributeur au grossiste.
Et ce phénomène s'amplifie au fur et à mesure que l'on remonte le long de la chaîne d'approvisionnement.
Comment optimiser une chaine d'approvisionnement ?
Quelles peuvent être les pistes d'actions, dans le cadre d'une démarche Lean, pour évoluer progressivement vers un mode d'approvisionnement idéal ?
Elles peuvent être de plusieurs ordres :
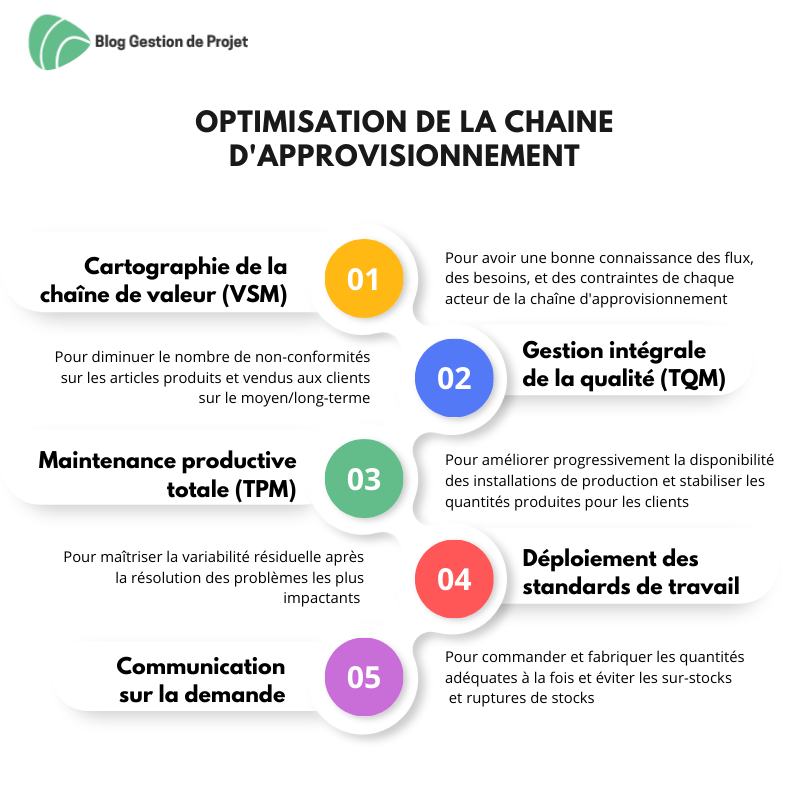
1. Cartographie de la chaine de valeur (VSM) intégrant les fournisseurs
L'une des clés pour le déploiement d'une démarche Lean efficace consiste à travailler de manière collaborative, en impliquant les acteurs concernés, plutôt que de fonctionner en silos.
Ceci est vrai à l’intérieur d'une entreprise, mais également en inter-entreprise, particulièrement lorsque l'on travaille sur la chaîne d'approvisionnement.
Afin d'avoir une bonne connaissance des flux, des besoins, et des contraintes de chaque acteur de la chaîne d'approvisionnement, un bon outil pour réaliser un diagnostic reste la VSM. Il s'agira ici de réaliser la VSM sur un périmètre intégrant les différentes entreprises concernées.
Une bonne pratique consiste également à réaliser les VSM en commun, c'est-à-dire que le client participe à la réalisation de la VSM sur la partie située chez son fournisseur, et le fournisseur participe à celle de la partie située chez le client.
2. Gestion intégrale de la qualité (TQM)
TQM signifie "Total Quality Management". Il s'agit d'une démarche consistant à mobiliser l'ensemble du personnel d'une entreprise dans un esprit d'amélioration continue de la qualité.
C'est une démarche sur le moyen/long-terme qui aura pour conséquence de diminuer le nombre de non-conformités sur les articles produits et vendus aux clients.
Elle va donc dans le sens d'une meilleure stabilisation et d'une meilleure efficacité des approvisionnements.
3. Maintenance productive totale (TPM)
La TPM (Total Productive Maintenance) est une démarche d'amélioration concernant les activités de maintenance.
Tout comme le TQM, elle consiste à impliquer l'ensemble du personnel en vue d'évoluer vers une culture de "prévention" des pannes plutôt que de "réparation".
Elle va ainsi permettre d'améliorer progressivement la disponibilité des installations de production, et donc de stabiliser les quantités produites pour les clients.
4. Déploiement des standards de travail
Une fois que les problèmes les plus impactants ont été traités, la variabilité résiduelle nécessite d'être maîtrisée par la mise en place de standards de travail.
Ces standards doivent être établis en impliquant les personnes concernées. Ils font ensuite l'objet d'améliorations au fil du temps, mais toujours de manière concertée.
L'impact positif des standards sur la variabilité concernera principalement les opérations menées manuellement.
5. Communication tout au long de la chaîne d'approvisionnement
Pour neutraliser l'effet coup de fouet décrit dans la section précédente, la bonne pratique consiste à échanger des informations précises sur la demande entre les différents acteurs de la chaîne d'approvisionnement.
Le distributeur a la responsabilité de s'informer auprès de son client lors des fluctuations de demandes, afin de comprendre si c'est un écart ponctuel ou une tendance de fond.
Il doit ensuite communiquer ces informations en amont afin que son grossiste puis le fabricant puissent réagir de la bonne manière.
Cela permet de commander et fabriquer les quantités adéquates pour à la fois éviter les sur-stocks et les ruptures de stocks.
Conclusion
D'une entreprise à l'autre, le niveau d'optimisation de la chaîne d'approvisionnement peut être très variable.
Une optimisation du flux en "Juste-A-Temps" s'appuie sur un certain nombre de fondamentaux du Lean qui doivent être déployés en amont. C'est donc une démarche qui s'inscrit dans la durée.
Dans tous les cas, l'optimisation des flux de production, en incluant les interfaces avec les fournisseurs et les clients, devrait figurer en bonne place sur la feuille de route de la démarche Lean d'une entreprise.
Elle nécessitera une forte implication de la Direction et une collaboration avec l'ensemble des acteurs concernés.